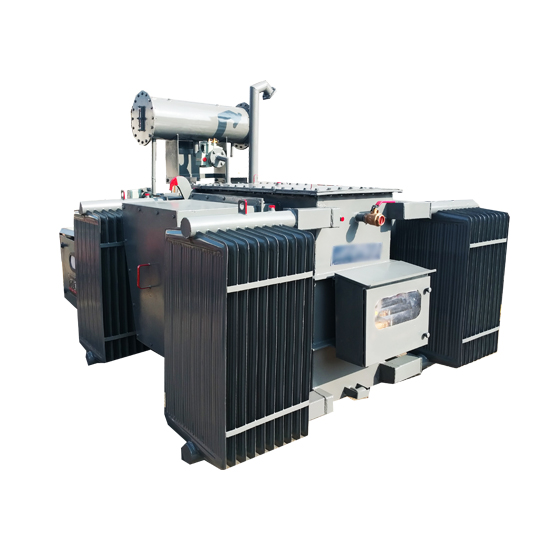
Furnace Transformer
We are Manufacturer, Supplier and Exporter of Furnace Transformer.
Features
- High Quality Imported Prime CRGO used
- EC Grade Copper & Aluminium used only HINDALCO make
- High Quality Transformer Oil Used IS:335-1993
- High Quality Complete In House Fabrication
- Temperature, Winding, Trip & Alarm sensors (on request)
- Epoxy Diamond Dotted Paper Used in Insulation
- Complete In House Transformer Designing
- Ease of service – design, installation, commissioning & maintenance all in one place
- Complete In House Routine Test Facility
- High Stock Levels kept for fast & time bound delivery
Product Description
Induction Furnace has coil constructed from heavy copper tubing. It is designed and tuned to the inverter circuit which applies a medium frequency (generally 500 Hz or 1000 Hz) voltage to the Induction coil. The magnetic field produced by the induction coil induces eddy currents in the charge and heats it. Medium frequency is necessary to enhance the rate of heat generation.
The inverter circuit requires for its operation a D.C. Voltage which is obtained by converting available three phase A.C. Voltage. Transformers which are used for transforming available three phase A.C. voltage to required voltage for converter circuit of the Induction Furnace are referred to as Induction Furnace Transformers. Thus they are essentially Rectifier/ Converter Duty Transformers.
Depending on the rating of the rectifier transformers, input voltage is derived from standard three phase AC distribution voltages like 433 V, 3.3 kV, 6.6 kV, 11 kV, 22 kV, 33 kV etc. These become the primary (or line side) voltage of the transformer. Secondary (or cell side) voltage can be between 400 to 1000 V decided by the required D.C. output Voltage.
These transformers must be designed to resist the high levels of electrical, thermal and mechanical stress to which they are subject during utilisation.
Other elements that must be taken into consideration when designing transformers for electric-arc furnaces are the high secondary currents required for the fusion process (dozens of kA) and the wide range of secondary voltages, which are normally regulated by an on-load tap changer (OLTC), either directly on the high-voltage winding or via an intermediate booster located within the same tank.
The furnace transformer thus has special features to handle such high currents as compared to conventional transformers. The electric arc furnace has 3 electrodes connected to the secondary terminals of the furnace transformers. The secondary terminals of the transformers are subject to frequent short circuits during the melting process through the charge and arc. Hence the furnace transformer needs to be specially designed to withstand the frequent short circuits.
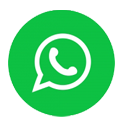
© Copyright Adhunik Electric Company. All Rights Reserved.